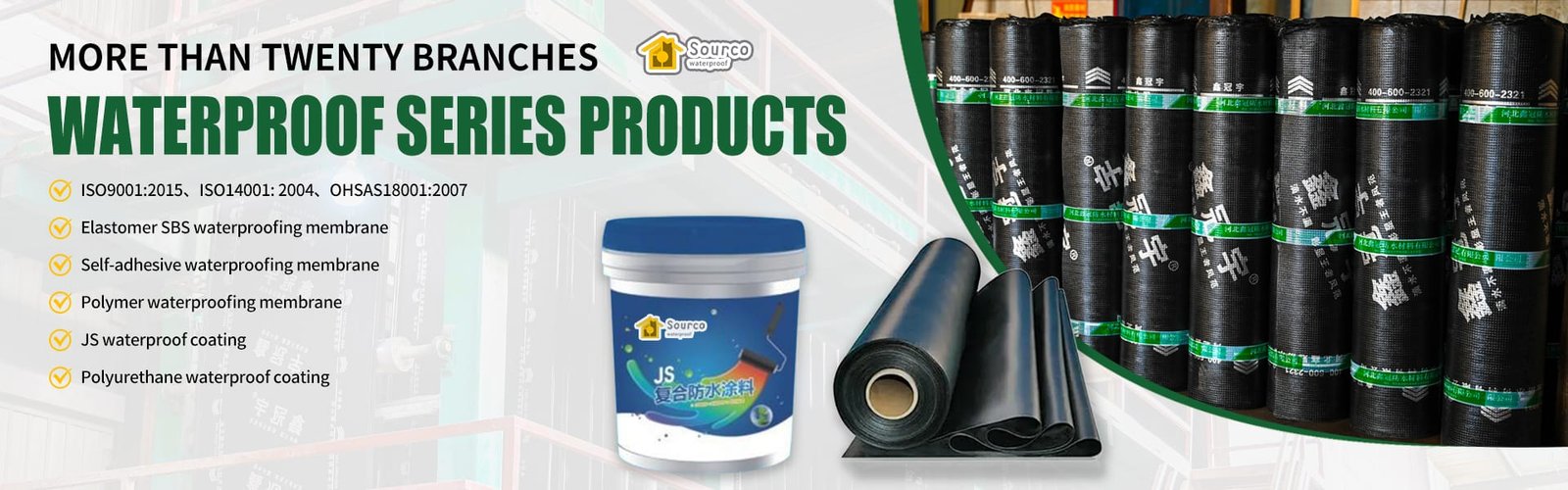
JS COMPOSITE WATERPROOF COATING
1.Non-toxic, Harmless, and Pollution-Free: Safe for use in drinking water projects and other applications.
2.Excellent Elasticity, Water Resistance, and Durability: The coating has high elasticity, excellent water resistance, and long-lasting durability.
3.Versatile Application: Can be directly applied to a variety of substrates, whether wet or dry.
4.Easy Application with Short Construction Time: Simple to apply and reduces construction time.
JS COMPOSITE WATERPROOF COATING DESCRIPTION
TECHNICAL PERFORMANCE INDEX SBS STANDARDJC/T894-2001
JS COMPOSITE WATERPROOF COATING Construction Conditions
Construction should not be carried out below 0°C or in rainy conditions. It is also not recommended to apply in extremely damp and poorly ventilated environments, as this may affect the coating’s performance.
JS COMPOSITE WATERPROOF COATING CONSTRUCTION TECHNOLOGY
Surface Preparation:
The substrate must be solid, clean, and smooth, with no standing water or leakage. Any uneven surfaces or cracks should be leveled first. If there is leakage, it should be sealed before applying the coating. Corners should be rounded.
Mixing:
Materials should be taken according to the chosen method and mixed thoroughly until there are no lumps or undissolved powder. The mixing time should be about 5 minutes, and it is best not to mix by hand.
Base coat ratio: Liquid material : Powder material : Water = 10 : 7 : 14
Other layers: Liquid material : Powder material : Water = 10 : 7 : 0-2 (water can be added or omitted depending on the actual situation)
Top layer: Pigments can be added to form a colored coating. The pigment weight should be no more than 10% of the powder weight. For sloped, ceiling, or vertical surfaces, no water should be added to ensure the coating adheres properly. For horizontal surfaces, more water can be added to ensure the coating remains smooth.
Coating Application:
Select the appropriate method based on the project’s requirements and follow the specifications. The curing time between layers should be based on the previous layer being dry and not sticky. Under normal conditions (20°C), the drying time for non-foot traffic areas is about 3 hours, and for areas with foot traffic, about 5 hours. In humid, low-temperature, or poorly ventilated environments, the curing time will be longer; conversely, it will be shorter in dry, warm, and well-ventilated environments.
Cleaning:
During breaks or at the end of the job, clean all tools and work clothes that are coated with paint using water promptly. Once the paint has dried, it will be difficult to clean off.
Quality Requirements and Project Inspection:
After the waterproofing work is completed, a thorough inspection of the project should be conducted. The membrane waterproof layer should be free from cracks, peeling, bubbling, wrinkles, or dripping. The thickness must meet the design specifications. Samples can be taken and measured with a caliper for verification.
Water Retention Test:
The test should be performed only after the coating has fully cured, typically requiring more than 48 hours. In non-ventilated and humid environments, the curing time may be slightly longer. For bathrooms and toilets, the waterproofing is considered qualified if no leakage occurs after 24 hours of water retention. After the roof waterproofing is completed, the drainage system should be unobstructed, and no leakage should be present for it to be considered qualified. (The test should be conducted after rainfall or continuous water exposure for more than 2 hours. If conditions allow, a 24-hour water retention test should be carried out.)
WATERPROOF COATING JS COMPOSITE APPLICATION SCOPE
Applicable to Various Substrates: It can be directly applied to various substrates, whether damp or dry (including brick, mortar, concrete, metal, various insulation layers, and waterproof layers). It is suitable for use on both new and old buildings and structures (such as basements, tunnels, bridges, reservoirs, swimming pools, etc.).
Roof, External Walls, and Bathrooms: It can be used for waterproofing on roofs, exterior walls, ceilings, and bathrooms.
Usage as Adhesive or Sealant: The material is mixed in a 10:7 ratio of liquid to powder to form a paste. It can also be used as an adhesive or sealant for materials like mosaics, tiles, etc.